Nas condições de desenvolvimento dinâmico dos processos da economia moderna, a criação de procedimentos de produção e controle cada vez mais complexos, uma das abordagens mais relevantes para o seu aprimoramento é a introdução de métodos para otimizar diversas perdas. Em primeiro lugar, trata-se dos recursos das empresas - temporários, financeiros, tecnológicos, energéticos e outros.
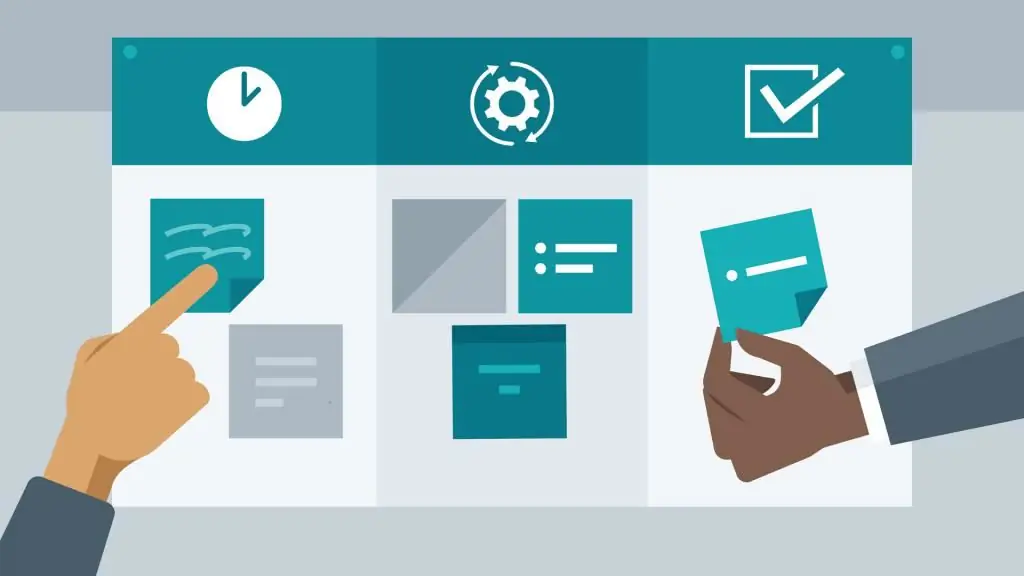
Características da atividade
Na prática, existe um certo teto, que está associado ao nível de desenvolvimento tecnológico e organizacional do sistema (organização, empresa). É claro que não é adequado exigir a automação total da produção de uma pequena oficina de alfaiataria de acordo com vários critérios e, sobretudo, econômicos. No entanto, independentemente do tamanho do sistema, é necessário garantir o máximo e ótimo uso dos recursos disponíveis com perdas mínimas, o que vale para qualquer organização e atividade.
Neste caso, torna-se necessário o uso de técnicas progressivas de gestão de processos que se baseiam na teoria da criação de produção enxuta ou "enxuta". Estes incluem sistemas 5S e TPM, mapeamento de fluxo de valor e SMED, etc.
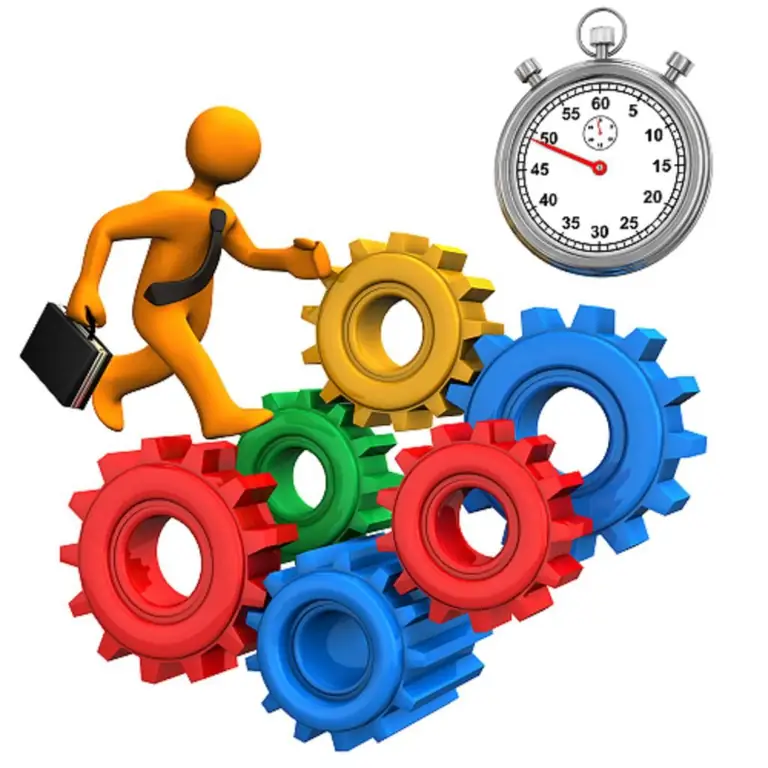
O propósito da inovação
A produção enxuta ("lean") é um sistema de abordagens especiais para a organização das atividades, que tem como objetivo principal a eliminação de diversas perdas no sistema. O mecanismo é bastante simples: tudo o que não agrega valor ao cliente deve ser classificado como redundante (desperdício) e retirado do sistema. É claro que o conceito de "perdas" é a pedra angular, pois sua definição afetará diretamente a eficácia do método. Nesse caso, aprender a mapear o fluxo de valor de seus especialistas é uma vantagem significativa no mercado de prestação de serviços
Tipos de perdas
"Lean manufacturing" é um dos conceitos fundamentais da logística de produção. E embora existam várias abordagens diferentes para determinar as perdas, vamos destacar os tipos mais universais:
- Tempo de espera - qualquer tempo de inatividade nas atividades reduz o valor do produto final. Aguardar materiais, reparos de equipamentos, informações ou orientação da gestão retarda o processo e aumenta o custo de sua implementação.
- Operações desnecessárias (processamento desnecessário de produtos) - operações tecnológicas desnecessárias, etapas do projeto, tudo o quefornecidos por procedimentos padrão, mas podem ser nivelados sem perda de confiança do cliente.
- Movimentações desnecessárias de trabalhadores - busca de ferramentas, equipamentos, movimentos irracionais devido à má organização do local de trabalho, etc.
- Movimentação desnecessária de materiais - má organização do sistema de estoque, f alta de mecanismos progressivos de logística de transporte e terceirização de logística.
- Excesso de estoque - imobilizando o capital de giro de uma organização como resultado de altos gastos com itens de estoque em excesso.
- Resíduos tecnológicos - sistemas de processamento de dados desatualizados, processos tecnológicos e rotas de processamento.
- Perdas por superprodução - a produção de uma quantidade excessiva de produtos, o que leva a um aumento no custo de armazenamento, transporte e posterior venda.
- Perdas intelectuais - f alta de mecanismos para estimular a iniciativa de trabalhadores e empregados, um sistema fraco de propostas de racionalização, supressão de uma abordagem criativa do trabalho.
Um dos métodos mais comuns para eliminar o desperdício do sistema e simplificar a execução do projeto é o mapeamento do fluxo de valor. A manufatura enxuta, ao mesmo tempo, permite que você crie um sistema adaptativo que responde de forma flexível às mudanças no ambiente.
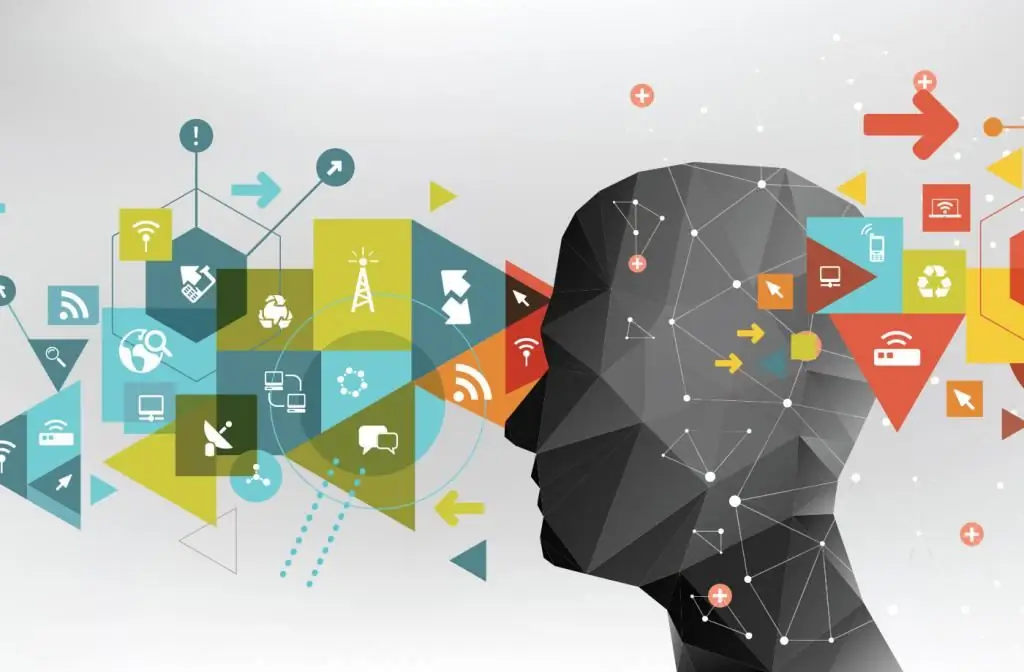
Value Stream
Value stream é um conjunto de todas as ações (operações) que são executadas em um produto para atingiro estado requerido ou obter as características requeridas. As ações são diferenciadas em dois grupos:
- criando valor do produto (adicionando valor);
- não agrega valor ao produto.
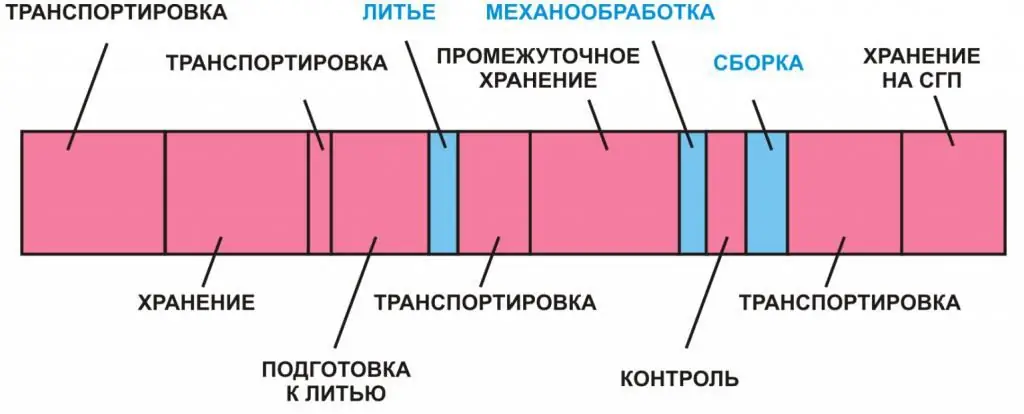
Como pode ser visto na figura apresentada, as etapas de mudança tecnológica do produto (cor azul) agregam valor ao produto, e as etapas de operações auxiliares - preparação, transporte, armazenamento - (cor rosa) - pelo contrário, reduza o valor do produto devido a perdas de tempo desnecessárias.
Processo de mapeamento
A base da técnica de mapeamento é o desenvolvimento de um algoritmo gráfico especial que mostra o processo de criação de produtos (implementação do projeto) no tempo. Esse algoritmo é chamado de mapa de fluxo de valor, que é um modelo gráfico baseado em um conjunto específico de símbolos (sinais, símbolos).
As principais vantagens do cartão:
- obtenção de um modelo gráfico do processo em andamento, levando em consideração vários processos adicionais para uma percepção visual holística (a tarefa é ver o fluxo geral de eventos);
- a capacidade de detectar vários tipos de perdas em todas as etapas do projeto;
- possibilidade de otimização paramétrica do modelo resultante para minimizar custos de todos os tipos;
- trabalhe com diversos indicadores do algoritmo, que se refletirão na melhoria de processos reais.
Formação de mapeamento de fluxo de valor com base em gráficos padrão esímbolos - blocos retangulares e triangulares, setas direcionais e escalonadas e outras figuras. Possibilita o registro das etapas do processo em estudo em um único idioma para todos os especialistas. Ao mesmo tempo, recomenda-se diferenciar os símbolos dependendo do fluxo considerado - material ou informativo.
Lean Value Stream Mapping permite identificar todos os locais onde os itens desnecessários se acumulam.
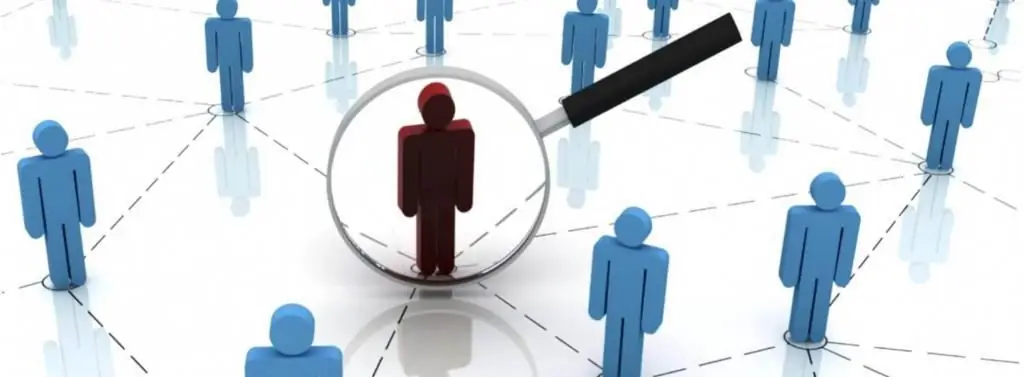
Regras de construção
Mapeamento de fluxo de valor envolve uma série de etapas simples que criarão rapidamente o modelo de projeto necessário com os parâmetros fornecidos. Por exemplo:
- Faça uma análise dos fluxos de materiais e informações para obter uma imagem confiável do estado atual do processo.
- Percorra os fluxos no sentido direto e reverso para identificar as causas ocultas das perdas e encontrar padrões negativos.
- Em qualquer circunstância, faça você mesmo as medições de tempo, sem depender dos resultados de outros especialistas ou valores padrão.
- Se possível, crie um mapa também por conta própria, o que tornará possível evitar erros de outras pessoas e soluções de modelo.
- Foco no produto em si, não nas ações dos operadores ou equipamentos.
- Construa um mapa à mão, usando um lápis ou marcadores.
- Visualize os elementos de um processo usando cores para melhorar a percepção.
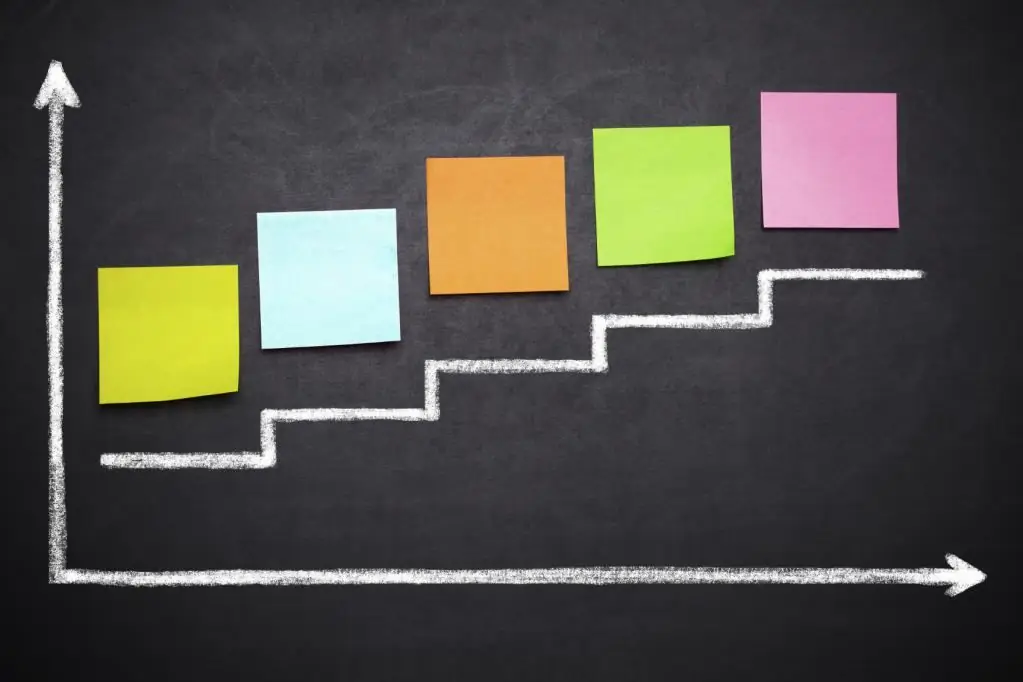
Exemplos de mapeamento de fluxo de valor
Vamos considerar um exemplo de criação de um mapa de fluxos no domínio da gestão documental, inerente às atividades de qualquer instituição.
A principal tarefa é escolher o melhor fornecedor. O processo de decisão padrão é o seguinte: seleção de um fornecedor (12 dias) - execução do texto do contrato (3 dias) - coordenação em serviços funcionais (18 dias) - visto de pessoa autorizada (3 dias) - obtenção do selo da cabeça (1 dia) - obtenção da assinatura da contraparte (7 dias) - registro nas autoridades (3 dias).
Total temos o tempo necessário para obter o contrato exigido - 48 dias. O resultado da análise foi a descoberta dos gargalos do esquema de tomada de decisão.
Principais alterações após análise do mapa:
- Foi emitida uma ordem para delegar a assinatura de parte dos documentos aos chefes de departamentos (reduzindo a carga sobre o aparelho administrativo e uma redução significativa no número de aprovações).
- Os mesmos requisitos foram desenvolvidos para todos os serviços (um entendimento comum dos requisitos para documentos contratuais, uma diminuição no número de erros por executores).
- O princípio de análise de documentação de ponta a ponta foi implementado através da criação de um grupo comum de especialistas de diferentes serviços.
- Usou novos modelos de contrato.
- Os mecanismos de processamento de documentação pelo sistema eletrônico foram otimizados.
- Foi desenvolvido um sistema eletrônico de acompanhamento da qualidade dos documentos que passam pelas etapas do processo.
Resultado principalo mapeamento do fluxo de valor tornou-se uma redução de 2 vezes no tempo de obtenção da documentação contratual, incluindo o tempo de aprovação nos serviços departamentais.
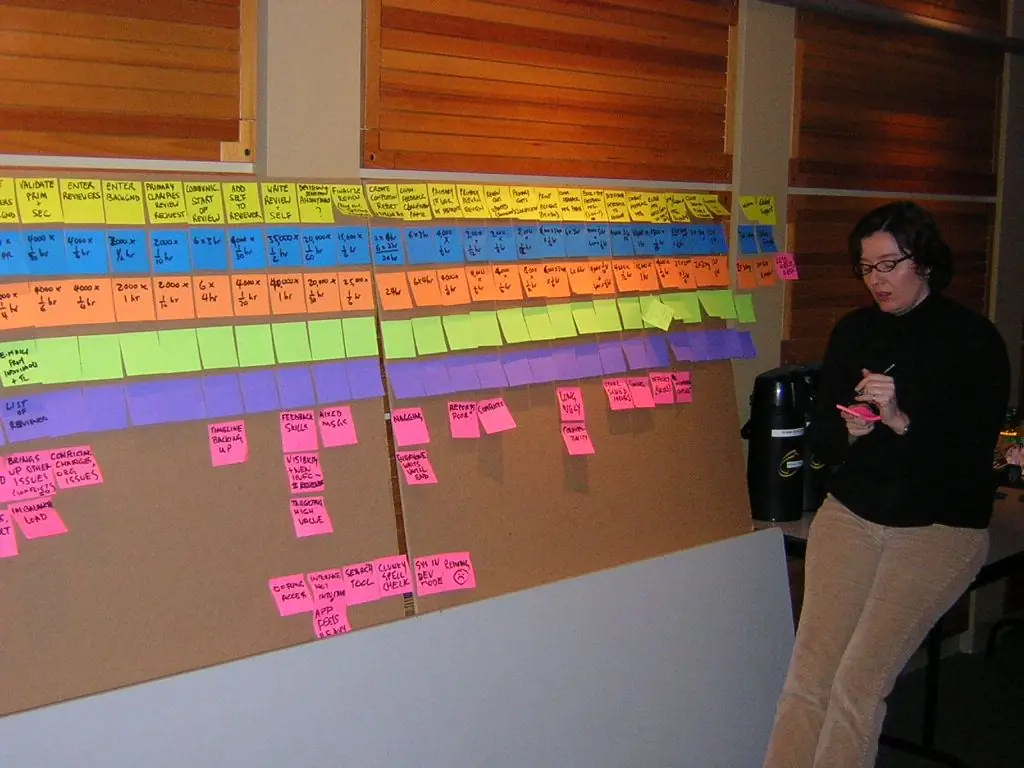
Conclusão
Recentemente, o mapeamento do fluxo de valor (VSM, Value Stream Mapping) tornou-se um método muito comum para otimizar o trabalho de várias organizações. Isso se deve à sua simplicidade e acessibilidade, custos mínimos com efeito benéfico acumulado ao longo do tempo. Existem muitos exemplos de implementação bem-sucedida desta metodologia básica de logística de produção: empresas da Rostec Corporation, Transmashholding, Russian Railways, etc. Recentemente, um sistema de manufatura enxuta foi criado em nível federal em instituições médicas. Em particular, propõe-se realizar mapeamento de fluxo de valor em policlínicas.
Como você pode ver, todo o potencial do método considerado está apenas começando a ser revelado.